What are the uses of steam in textile?
Steam utilization in the textile industry is steam energy used for fibre production, weaving, dyeing, drying, printing, ironing, washing, heating the equipment, and the temperature of the machine sheds. Also, many other industries and manufacturing processes use steam as, a heat source and for cleaning and sterilisation. So producing steam energy consumption saves money. Steam systems are also common in the manufacturing of food and meat processing, in commercial laundries and also in hospitals
The steam generated by boilers may be utilized in textiles for the following purposes textile,
- Steam is seldom used for power generation
- It is used for general heating and air conditioning of all the premises.
- Steam utilization in textiles, as steam is specially used for process purposes such as sizing, dying bleaching finishing and printing sections
Steam used in sizing
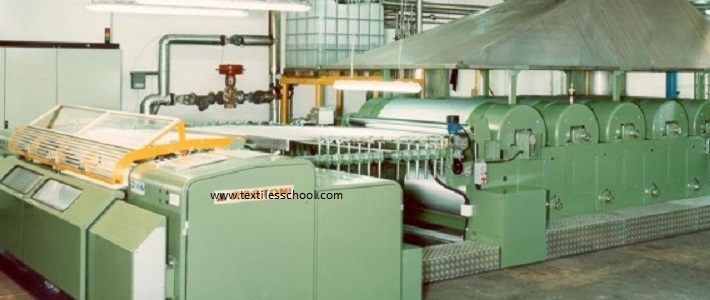
In the case of sizing steam is used as a medium for keeping the size at an elevated temperature to maintain the size liquor viscosity constant. At 190~2000F best results are detained giving fairly stable viscosity. Temperature controls up to ±20F can be obtained by using an automatic thermostatic element operating a valve placed on the main steam supply. Steam from the boiler is reduced to a pressure of 5~10 PSI before being admitted in the size.
Drying is also done through the medium of dry steam at suitable pressure which is supplied to a big cylinder over which the warp sheet passes. For most efficient drying the outer temperature of the cylinder drum is kept reasonably constant.
Steam utilization in the dying department
In dying heat is required to liquor to the required temperature and also maintain the temperature for a specific period of time.
Steam is often used to maintain the viscosity of a caustic soda solution for bleaching and scouring purposes. The steam can be introduced at 5 PSI on a low-pressure basis or rarely exceeding 30 PSI for high-pressure printing. The closed steam coil or direct system of the liquid solution may be adapted. But now a day outside multi-tubular heaters are used.
Steam utilization in textiles in the finishing department
Steam is an essential part of textile printing and consists in submitting the printed pieces to the action of steam for various lengths of time and at various pressure. This process expedites the relaxation shrinkage and affects the decomposition of various moderate. And their subsequent combination with the colouring matter with which they are mixed.
In the case of “continuous steaming” large quantities of cloth are made to travel slowly in an enclosed steam atmosphere. Here both pass continuously through the streaming chamber in the form of loops supported on brass rods and carried forward by an endless chain. The automatic ageing and steaming machine can deal with all types of printing requiring exposure to steam to develop colours.
Some definitions of steam
Following are the main definitions before studying in detail the steam properties.
Enthalpy of water
“The amount of heat absorbed by 1 pond of water is being heated from freezing point to boiling point at a constant pressure is known as enthalpy of water” i.e
00C → 1000C (enthalpy of water)
Also, enthalpy depends upon the pressure under which water is heated.
Latent heat
” The amount of heat absorbed by 1 pond of water in being a conversion from boiling water to steam at a constant pressure is known as latent heat” i.e
1000C → steam (latent heat)
Wet steam
“The steam which contains small particles of water in suspension is known as wet steam or vapour“.
All steam is wet while it is content with water from which it is being raised.
Dry or saturated steam
“The steam containing no suspended water particles is known as dry or saturated steam”
Dryness fraction of the steam
” The ratio of the weight of the actual dry steam to the weight of wet steam is known as the steam dryness fraction ” i.e
Dryness fraction=weight of saturated steam /weight of wet steam
Explanation
Imagine one pond of water at a temperature of 00C to be heated in a container under constant pressure. The water will absorb the heat supplied until it starts boiling i.e 1000C at standard temperature pressure. If the heating of this water is continued there will be no further increase in temperature. But the heat will be utilised to convert the water to steam. This will be wet steam and need to be further heated to become saturated. At this saturated state, the whole heat supplied will be absorbed. But the temperature of the dry steam will be the same as that of the boiling point temperature.
Superheating
” If the dry steam in gas form is further heated at the same constant pressure, the temperature will begin to increase, this heat of dry steam above the temperature of formation is known as superheating”
Steam purity/quality of steam
Hence, steam purity or quality of steam is calculated as a measure of saturated steam that coexists with condensate within a given system” dividing the mass of steam by the total mass of steam and its condensate
Impurities are of two types
- Mechanical carryover ( impurities carried with liquid droplets)
- Vapour carries over (impurities carry with steam)
Generally, steam impurities increase with steam pressure
Also, impurities present in steam have a very minor to shallow effect on textile processes
Steam purity
Steam purity can be calculated as 0~100 steam quality. Means of 100% liquid(condensate) and 100 pure steam mean of 0% liquid condensate.
B.T.U
“The average amount of heat required to raise the temperature of one pound of water through 10F is called 1 B.T.U“. B.T.U mean British thermal unit.