Enzyme washing or “bio stoning” is a textile finishing process or technique in which enzymes are applied to denim or fabric to get a special look, such as stone washing, a softer feel, or a vintage or weathered look. The weathered look effect is produced by enzyme washing mostly by using cellulose enzyme-modified natural or acidic pH or some, mechanical agitation such as steel balls. These enzymes are live cells, freeing dye or breakdown fiber of fabric from fabric or garments. to achieve a faded appearance or a softer feel. Enzyme wash is used in indigo denim, in these cases, enzymes are replaced by stone washing with better results with whiter and bluer color contrast. These enzymes are relied techniques in biotechnology which is called also bioprocessing or bio finishing. The enzyme wash finishing however is more costlier than the stone wash process.
Moreover, in the modern world sustainable eco environmentally friendly, fully biodegradable, and nontoxic enzymes are of increasing importance and interest. This enzyme treatment process replaced several chemical and mechanical treatments to get improved quality and comfort.
History of Enzyme Washing
At the start of the 80s environmental effects of stone washing drove a demand to search for sustainable methods for washing effects. The first enzyme wash method was introduced in 1989 in Europe and later years followed in the United States. Novozymes developed a spray technique directly on denim fabric significantly reducing water consumption in the enzyme wash process. ch as enzyme washing is even more integral to the textile industry.
Enzyme Wash Advantages
The usage of cellulose enzyme has many advantages, such below as:
- Cellulase enzyme is more sustainable over stone washing use of pumice stone or acid washing use of excess water. The residual pumice stones and acid produced more wastewater to eliminate. Also, enzyme wash treatment reduces the percentage of fabric damage The denim fabric ensures less water use not need multiple washes resulting in less waste and damage to machines. In concise words, this process is more sustainable, and ecofriendly.
- Can be recycled enzymes to reuse,
- Enzymatic treatment produces denim or garments with more softer feel and better appearance.
- The productivity of washing load increases as no use of pumice stone to get effects.
- Cellulase enzymatic treatment is more efficient as the residual or fragment of stone from denim jeans is time-consuming.
- The number of after-washes reduces significantly.
Enzyme Wash Disadvantages
- In enzyme washing, Dye released by enzymatic activity tends to redeposit on the denim fabric called back staining in enzyme washing. However, some denim wash treatment specialists agreed that are not detectable to normal users. To remove back staining garments need to be rigidious washed.
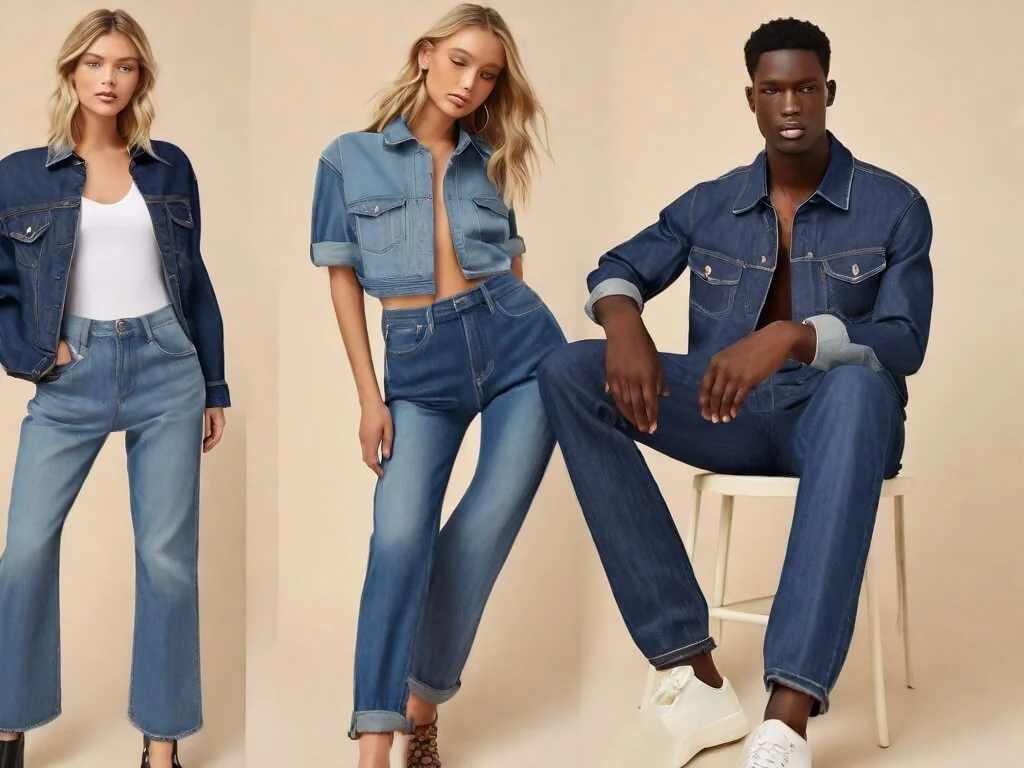
Enzyme Washing Process
In the enzyme treatment process, the temperature is most important as these enzyme reactions are limited to a temperature range. Enzymes are sensitive alive which below 15°C and 60°C reduce their activity sharply. However there is a color fading effect when rising in temperature but within range, so more fibers are hydrolyse and fiber are removed by abrasion of fabric.
The mechanical action provides a fading effect to color in enzyme washing. The fabric treated without any agitation has better color fading and a softer effect rather than agitatuin because weekend fibers will not removed providing a more hairy and fizz layer on the cloth surface.
For fabric processed under hard agitation, an effect called biopolishing is obtained. The strong mechanical agitation causes weakened fibers to be well removed, Thus a smoother and cleaner surface is produced. Also, the resultant fabric has a more faded shade as dye particles are also removed with fibers.
For further abrasion prolonged treatment time for degradation of cellulose is required. Also, the color fading effect increased. The weak dye particles are desorption and are weakly absorbed into fabric or garments. Cellulase heavily hydrolyses fragments of cotton fibrils and thus produces a fabric that is less fuzzy than the original when treated longer time.
Flow Chart of Enzyme Wash Process
Hydrolysis of the cellulose enzyme is used in treatment, which is catalyzed so the surface fibers loosen and get removed when further treatment. Such as fabric-to-fabric abrasion or fabric-to-stone abrasion during the washing process. The temperature and pH were kept specific to the enzyme. Usually, 6~7 pH is applied for neutral and 4.5 to 5.5 for acidic by adding Acetic acid (CH3COOH). An enzyme dose of 2~4 grams/liter is sufficient. Generally color of enzyme-treated denim is more uniform when not added any stone.
A step-by-step enzyme wash treatment is as below
Denim fabric or garment loading
↓
Desizing or starch-washing removal
↓
Rinse two times
↓
Insertion of an enzyme to wash
↓
Adjusting enzyme PH
↓
Set temperature according to enzyme
↓
Tumbling wash time depends upon the required shade or effects
↓
Rinse two times
↓
Softening agent
↓
Unloading
↓
Drying process
The enzyme wash process consists of 4 basic steps are;
- Desizing
- Bio-abrasion
- Back was
- Additional Bleaching
1- Desizing
The first step of enzyme wash is de-sizing. In this step first, dust, or other impurities are removed from garments or denim fabric. This step is also used as a wetting agent.
- Water L: R = 1: 5
- Temperature: 50°c to 70°c.
- Add desizing agent 0.5 to 2 mg/liter.
- Add wetting agent 0.2 to 0.5 mg / liter.
- Duration 10 to 15 minutes.
- Wash the second time with cold water.
2- Bio-abrasion
In this step, enzymes are added to remove coloring to get faded denim. If desired more fading then add stones half the volume of garments.
- Water L: R = 1: 5
- Enzyme 0.6 to 2% according to the required results
- Maintain pH 4.5 to 5.5
- Anti back staining 2 to 2 mg/liter.
- Temperature: 50°c to 55°c.
- Time: 50 to 95 minutes.
- Wash the second time with cold water.
3- Back Wash
In this step, all the enzymes that are dead now are removed with coloring material from the denim or garments. Dye again fabric by a rise wash by the process as
- Water 1: 5
- Add anti-back staining agent 1 to 3 mg/liter.
- Add soda ash 0.3 mg/liter.
- Temperature: 75°c to 85°c.
- 5 to 10 minutes.
- Rinse normal.
5- Additional Bleaching
If any extra fading effect is needed then this step is done by following. Chemical use to resist the yellow effect on denim.
- Water 1: 5
- Add sodium Meta bi-sulfite 1 to 2 mg/liter. Also, sodium hypochlorite 5 to 5 mg/liter.
- Temperature: 45°c to 55°c.
- 10 to 20 minutes.
- Normal remise
Load the garment to the hydro extractor and then to the dryer.