What is Digital Textile Printing?
Digital textile printing is a method where colorful designs are embossed on fabric using ink-jet printing technologies. It is one of the valuable developments in the textile printing industry which maintains high standards of quality. Also, digital printing opens a new way for the growing demand in the textile printing industry. Digital printing does not require any screen or color limitations. Also, ideal for 3D designs. Using this technology can be printed on fabric, digital printing t-shirts, jeans, etc. However in rotary screen printing and flat screen printing color limitations up to 1~20, usually more than 12 colors are not printed due to reasons: 1- High print cost, 2- Machine complexity. Also, 3D designs and effects are not possible with other methods, such as over digital printers.
In today’s world, technologies are evolving. Digital printing was first patented in years 1968. Also, it started gaining popularity in 1990. About 60% of digital printing in total is done in Pakistan, Bangladesh, Indonesia, India & Vietnam. One of the industries that has benefited from cutting-edge technology is the fashion industry. Digital printing on fabric, designers, and manufacturers now have new opportunities for garments. Digital printing on fabric is a process that uses specialized printers. To directly apply vibrant, high-resolution designs on fabrics. Unlike traditional screen printing which requires multiple steps. Digital printing offers a more streamlined and efficient approach.
Understanding the Process of Digital Printing
Let’s take a guide and fully understand the process behind it, and how digital textile printing technology works. A line of process as below,
- Selection of fabric
- Design development
- Fabric preparation
- Ink selection
- Printing
- Heat fixation or cure
- Washing
Selection of fabric
The first step is to select fabric for digital printing. All fabric types like cotton, viscose, linen, etc. are suitable for this printing process. Select the appropriate fabric whether it’s apparel, home décor, or a commercial use fabric.
Design development
The second task for digital printing is to create a design according to requirements. A design artist or simply say developer creates design with the help of graphic design software. It may be like Adobe Photoshop (sometimes Adobe Illustrator) and the CYMK color model is used as the basic or any other software available using a computer. TIFF files are generally used for good-quality artwork results by designers for printing. Also, the scanner can be used if layout or hand artwork is available and can be converted to digital format. Now these images on your computer screen are ready to transfer on fabric.
Fabric preparation
Use pretreatment of fabric with the chemical solution before going to print. Pretreatment enhances the absorbency and improves the color vibrancy of the print. Generally, ink-jet printing with reactive dyes as for cotton or viscose, a thickener, alkali, and urea process is used to accept the dye or ink for better absorbency. Treated fabric is more crushes and makes it suitable for feeding to the printer.
How to select Ink?
Selection of digital textile printing inks is a crucial part, as the question is what kind of ink should be used? Ink selection depends upon the types of fabric, different fabrics require different inks. Some common types of inks are used details as below:
- Acid and reactive ink: These are dye-based inks, used for natural fibers. This dye ink penetration in the fabric is good, also, the hand feel and color washing fastness. But make this ink several steps required like pre-treating, heating, washing, and steaming.
- Pigment ink: It is mostly used for natural and synthetic fibers fabric like 100% polyester, blended with poly, Cotton, Rayan, and Silk. There are up to 8 colors in pigment ink CMYBGOVR (Cyan, Magenta, Yellow, Black, Gray, Orange, Violet, and Red).
- Disperse ink/ sublimation: Sublimation ink is used to make signage, sportswear, and banners where fabric is typically spandex or polyester. Color range available up to 15 colors in a set. Transfer of sublimation ink to fabric directly or with the help of receptive paper.
- Printers & printing: Most often digital textile printing technology uses inkjet printer technology. The fabric after pretreatment fed to a digital printer where it is sprayed by small droplets nozzle according to design and software. Calibration is an essential step to ensure accurate and quality color production. Regularly calibrate your printer to maintain consistent and reliable results. Fabric should be at proper tension and precise position to control crimps and to avoid distortion during the printing process. causes misprint. Then set printer heat concerning width and thickness. There are many kinds of digital textile printing machines available as,
Digital textile printing inks characteristics Ink Fabric Type Pre-treatment Post-treatment Pigment Natural, Synthetic No (Usually) Dry heat Acid Wool, silk, Nylon Yes Steam heat Reactive Cotton, Rayon, Silk Yes Steam heat Disperse Dye Polyester yes Steam or dry heat Disperse sublimation Polyester No Dry heat transfer
- Direct-to-textile printing: With the help of inkjet technology printers directly transfer ink to the garment or directly to the fabric. In this type most detailed artwork and design print are possible. These methods can print on different fabric types such as cotton, silk, and nylon.
- Disperse dye sublimation: In this method steam or heat is used for dye fixation. Also, this method eliminates the need for transfer paper for printing. In this case, the fabric is pretreated before use and this technique allows for two-sided printing.
- Sublimation printing: It is a modern technique that is used for polyester fabric. In this process, dyes are converted to gases by applying heat and pressure attached to the fabric surface which is polymer-based, as polyester. It is used for small production and allows highly detailed work.
Heat fixation or cure
After printing, we need to fix the design. It depends upon the type of fabric and ink used. Methods used for fixing treatment are
- Pigment ink: Used dry heat usually heated calendar roll or heat press.
- Acid dye: Used steam and wash then dry methods
- Dispersed dye/ Sublimation: generally dry heat, calendar roll, or heat press is used in large industries.
- Reactive dye: Used steam and wash then dry methods
Washing
Lastly, the fabric is washed and dried properly.
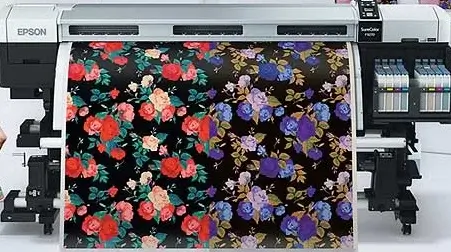
Advantages of digital printing on fabric
- It gives greater color versatility. Also, there is no color limitation, so, highly detailed artwork and better color quality can be attained.
- No need for a screen during digital printing. So, another significant advantage of digital printing on fabric is its speed and efficiency. Unlike screen printing, which requires the creation of separate screens for each color, digital printing allows for faster production times. Designs can be printed directly onto the fabric in a single phase. Reducing the overall production time significantly.
- Less capital investment concerning other textile printing types.
- Digital printing offers environmental benefits. Traditional screen printing often involves the use of harmful chemicals and excessive water consumption. In contrast, digital printing uses minimal water-based, eco-friendly inks. Furthermore, makes it a more sustainable and eco-friendly method of fabric printing. It also aligns with the growing demand for environmentally friendly practices in the fashion industry. Digital textile printing technology uses of water is 90% less. Also, the consumption of electricity is 30% lower than a traditional printing process.
- Less wastage of dyes/inks and chemicals than screen printing types.
- Requires less manpower than traditional printing.
- In digital printing, there is no need to do any calculation of repeat design. Designs are built on a computer.
- Design can be developed with high resolution (300-1200 pixels/inch). So that, printing quality is higher.
- No need for screen engraving.
- Lower sample cost of digital textile printing.
Limitations of digital textile printing
- Lower in production for high-resolution fabric design. Also, production depends upon machine heads. As general production rate is 3~4 meters per minute maximum.
- Digital printing production cost is very high.
- Digital printing uses sensitive electronics that can operate at room temperature not more than 250C. Also, ink can coagulate and may damage the printer.
- Blended fabric types are not possible to print.
- In the case of digital textile printing, printing is not done on deep color.
Screen printing vs Digital printing
Traditional screen printing types have been adopted method for fabric printing for years. But, digital printing has emerged as a chilling competitor. The digital printing method has several advantages. Since, that makes it a preferred choice for many designers and manufacturers.
If you are looking for types of textile printing, which is a subject itself, check out the post “Types of Printing-8 Best Textile Printing Techniques“
Screen printing vs Digital printing | |
Digital printing type | Screen printing type |
1- Digital printing is a modern, computer-controlled process. It directly transfers a digital image or design onto the fabric. | 1- Screen printing is an older, manual process. That pushes ink through a stencil or screen on fabric. |
2- It uses inkjet or laser printers to apply ink. It allows for high-resolution and intricate designs. | 2- it is a more hands-on process. Also, it is particularly well-suited for simple designs. Use fewer colors in the design. |
3- Digital printing can reproduce a wide range of colors. So, this makes the design ideal for full-color and photorealistic. | 3- Screen printing, the number of colors in a design is usually limited. |
4- It can achieve effective gradients and shades. | 4- Complex color gradients and photorealistic images are challenging. |
5- Digital printing is cost-effective for short runs. | 5- Screen printing is cost-effective for large quantities. |
6- It is not as cost-effective for large runs. Because of the high ink costs. | 6- It can be expensive for small runs. Not cost-effective due to the large setup, also, screen preparation, and color separation. |
7- Digital printing produced consistent results, with minimal variation in prints. it is highly automated. | 7- Screen printing may have slight variations between prints. Depending on the manual screen tension, and ink application. |
8- Digital printing is versatile in use. It is suitable for a wide range of substrates, including fabrics, paper, plastic, etc. | 8- Screen printing is suited for fabrics. So, it can handle thick or uneven surfaces like glass, etc. |
9- The durability of digital prints is a question mark. It is not so long-lasting. | 9- Screen printing is more durable and long-lasting. |
Faults of digital textile printing with remedies
Color Staining
Causes: Color appeared in non print area. Especially in dark-color printing.
Remedies: The coating recipe should be suitable, also during drying or steaming fabric should not co-contact with the ink area.
White Spot
Causes: uneven singeing.
Remedies: Pretreatment Remove the fabric surface properly before coating.
Low Color Yield
Causes: Uneven mercerizing and singeing. Unsuitable coating chemical.
Remedies: The singing and mercerizing process should be done properly before applying a coating. Also, use suitable coating chemicals.
Shade Variation
Causes: Printing the design accurately with the correct shade. But after finishing getting shade variation. It is mostly observed in digital textile printing. It is due to improper finishing parameters or chemical coating.
Remedies: focus on the chemical recipe, viscosity, and PH of the solution. Also, steaming and washing parameters should be proper.
Exploring various applications of digital printing on fabric
This technology opened up new horizons from high-end fashion brands to small-scale designers. Digital printing on fabric is a fashioning of unique and personalized garments. With digital printing, designers can design such as photographs, names, or patterns. This is a new age growing demand in the fashion industry.
Another application is the production of vibrant design. Eye-catching print designs make it ideal for bold and striking designs. Since to catch the attention of consumers.
Digital textile printing technology cost factors
Digital printing on the fabric is important to understand some overall cost factors.
One factor is the complexity of the design. Intricate and deep color designs require more ink. Also, time to print results in more costs. Simple and fewer elements and colors are more cost-effective.
The choice of fabric is another role in cost competition. Some fabrics may require extra pretreatment. Also, needs specialized ink. Some fabrics may require special handling too. All causing higher costs.
The choice of fabric quantity is a third factor. Digital printing is feasible for low-batch production. But if tried for larger quantities may be definite cost effective.
Lastly, the choice of printer is another factor. Different companies may offer structure, prices, and equipment. Twice think before selecting a printer with various companies keeping in mind quality too.
Digital textile printing market size & growth globally
Top digital printing on fabric companies
Several companies are leaders in the textile industry. These companies offer exceptional quality and expertise. Also, a wide range of printing options too. Since, making them top choices for designers and manufacturers. Here are companies known for their contributions to digital textile printing technology.
Printer company | Made |
1-Epson | Italy |
2-Kornit | American |
3-Roland DG | Japan |
4-Mimaki | Japan |
5-Durst | Italy |
6-MS Printing Solutions | Italy |
7-Zimmer | Germany |
8-Atexco | China |
9-EFI (Reggiani) | Italy |
10-Homer Digital |
China |