Humidification
The process of relative humidity central in any textile mill or department is known as humidification in textile mills. A controlled atmosphere is vital for the textile industry because humidification greatly affects the quality and production of finished goods.
Why is humidification needed in the textile industry?
The humidification of the atmosphere or moisture present in the air plays a very important role in textile industries. It affects the manufacturing process as well as working conditions and also human bodies. The following point indicates the importance of humidification.
Reduction of static charges
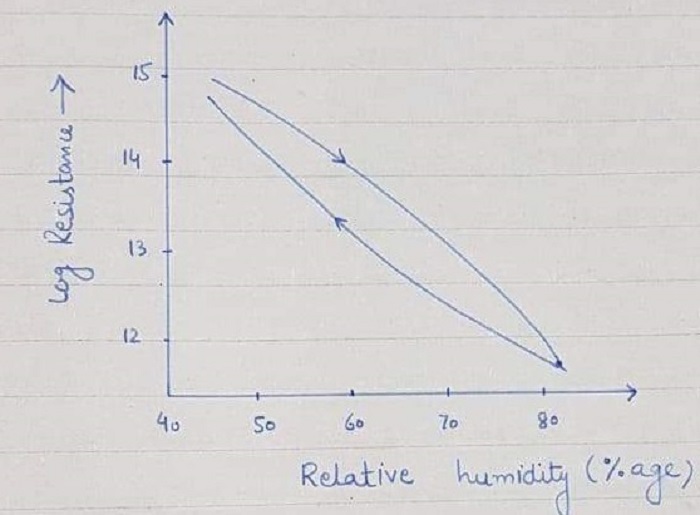
- Firstly adequate Humidification in textile mills is essential to eliminate the trouble from static electric charges caused by friction of raw material (cotton, wool, man-made fibers, etc) in the machine parts. So, these static charges cause fibers to repel each other in the process, stand out from the web separately, and become suspended in the air as a fly. Thus adequate humidity nullifies this effect by providing a short circuit. e.g. as shown by the laboratory curve for wool, the electrical resistance decreased approximately 1/100 of its value by increasing the relative humidity of the atmosphere through air conditioning from 45% ~ to 80%.
- Secondly, with appropriate humidity in the shed dirt and dust, and Lint is reduced.
- Another key point is proper humidity levels in the shed result in pliable, extensible, and stronger yarns. So, appropriate humidification in textile mills results in less friction and less yarn breakage which allows an operator to attend to more machines resulting in an increase in production.
- Decreased lint also results in good working conditions in the shed and there is a better effect on human beings.
- Additionally in weaving controlled humidity decreases the expansion and contraction of shuttle boxes, leathers, and other hygroscopic parts.
- Finally, the fabric produced in controlled conditions has a better appearance and more strength.
- The variation in humidity and moisture content during processing increases the variation in yarn count which is strictly undesirable.
Thus in order to get the best result throughout the year in textile mills, the recommended humidity levels should be maintained
Cotton yarn | ||
Process | Temperature in 0F | R.H percentage |
Blow room | 90~105 | 48~53 |
Carding | 90~100 | 50~55 |
Combing | 85~95 | 60~62 |
Roving | 85~95 | 55~65 |
Spinning | 70~80 | 60~70 |
Weaving | 65~75 | 70~80 |
Hosiery | 65~70 | 70~80 |
Yarn conditioning | 80~100 | 90~95 |
When relative humidity high
When relative humidity is high fibers tend to lap and stick on rollers in the fiber production process, moreover it can lead to loss of production efficiency and increased wear of machines. On the other hand, when humidity higher side fibre damage in the production process is reduced, as when increased moisture content level in fiber (high humidity ) increases its strength.
When relative humidity low
When relative humidification in textile mills on the lower side lapping on the roller can be controlled or minimized but also production efficiency can also be reduced as fiber strength will be lower due to fewer moisture contents. Also in low humidity static charges within fiber increase friction due to which fiber will be more brittle and damaged in the production process
So always maintain optimum level keeping in mind all factors.
Humidity control
Humidity is controlled by direct or indirect methods.
Direct method
In a direct system, separate local humidifiers add moisture to the air in the room.
Indirect method
But in an indirect system, separate local humidifiers add moisture to the air in the room. In an indirect system, the room receives moist air from the central filtration plant of air conditioning through ducting and diffusers
As a general practice, the spinning departments have separate humidifiers for each section e.g. carding, combing, ring, etc. These comprise essentially axial flow fans, filters, water tanks, spray chambers, heaters, and sometimes chillers. All in all the humidified area is distributed in the section through overhead ductwork and diffusers. Also, return air is normally taken along with the fresh air at the fan inlet. This may also be assisted by a direct system where needed.
In the case of the weaving section, the humidity level is greater than for other departments. If a central air conditioning plant is supplying conditioned air to the weaving department, it may not suffice the requisite humidity level and moisture is invariably added by localized direct humidifiers. So there are three types of direct humidifiers described normally as
- Simple spray type
- Enclosed spray type
- Disc humidifier
There are also many other types of humidifiers to give localized areas of concentration.
Advancement in humidification in textile mills
As well as technologies mature every day the technique of humidification changes in terms of efficiency and cost. For example, a few years earlier there was water sprayed from the nozzle but the fog system in the air conditioning plant is adapted which is much cheaper than the old ones. Some list techniques are as under
- Fog system
- Impeller new design which can save electricity.
- Thermally operated air conditioning is the newest one which is used commercially in small buildings