Man-made fibres are those that man has generated the fibres for himself from something which are not previously in a suitable fibrous form or from chemical reactions.
Classification of man-made fibres
In the classification of textile fibres, man-made fibres can be further subdivided into two main classes.
- Synthetic fibres
- Regenerated fibres
Synthetic or pure man-made fibres
- Nylons
- Polyesters
- Acrylic fibres
- poly urethanes
- Poly olefines
- Polyvinyl derivatives

- You may also like the post “Dyneema fiber an overview“
- You may also like the post “How to identify fibers in your mystery fabric piece“
Regenerated fibres
- Casein fibres
- Viscose rayon
- Acetate Rayon
- Cuprammonium rayon
- Alginate fibres
- Cellulose triacetate
Synthetic fibres or pure man-made fibres
synthetic fibres are those in which man has performed the entire work for the production of fibres. Altogether those fibres are obtained from simple chemicals which are derived from coal or oil. Also, these chemical has been made into materials capable of forming fibres. So, Man-made performed the entire work and nature had no hand in production at all. Shortly they are truly synthetic fibres this group includes
- Nylons
- Polyesters
- Acrylic fibres
- poly urethanes
- Poly olefines
- Polyvinyl derivatives
Nylons fibre
Nylons are of two types
- Nylon 6
- Nylon 6,6
Nylon 6
The raw material used for Nylon 6 is caprolactam, which is containing 6 carbon atoms, so it is card nylon 6. It is polyamide due to the repetition of NH2. Also, it is a linear polymer obtained by self -condensation.
(CH2)5—CO—NH2→ -H2O, 〈–OOC—(CH2)5—NH3+〉
Caprolectum→ Caprolectum salt
HNH—(CH2)5—COOH + HNH—(CH2)5—COOH → –H2O, H—⌈–HN—(CH2)5—CO-NH-(CH2)5-CO-⌉–OH
The viscosity of the polymer describes the molecular weight of the polymer. Also, the stretching of polymer is called Orientation.
Properties of Nylon 6
- Tenacity 8 gram/denier
- Elongation at break 16~20%
- Moisture regains 4%
- It is resistant to light but on prolonged exposure, has a gradual loss in strength.
- Softening temperature 170~1800C
- Ironing temperature 100~1300C
- It is biologically resistant and surely insects have no effect on him.
- Strong acids dissolve it, but not affected alkalies and weak acids.
- Organics like chloroform, acetone, and tetrachloride also have no effect on nylon 6, but dissolve in phenol, meta crezol.
- Trichloroethylene is used for its dry cleaning in foreign countries which has no effects.
Nylon 6.0 uses
It is used in garments, sports goods, knitwear, also fibre clothing, tyres, shoes, umbrella, bed sheets, curtains and cushions etc.
Nylon 6,6
The raw material used for nylon 6,6 is adipic acid and hexamethylene diamines. It is called nylon 6,6 due to the presence of 6 and 6 carbon atoms in raw materials.
H2N (CH2)6-NH (hexamethylene diamines)
HOOC-(CH2)4-COOH adipic acid
HNH-(CH2)6-NH+HOOC-(CH2)4-COOH→H-⌈- NH-(CH2)6-NH-OC-(CH2)4-CO-⌉n -OH
Catalyst CH3OH .1 .2%
T=2800C or t >2400C
t=3~4 hrs
P=35 kg/cm2
Properties nylon 6,6
- Tenacity 3~10 gram/denier
- Melting point 250~ 2520C
- Elongation at break 16~65%
- Specific gravity 1.14
- Moisture regains 4.5%
- It is not affected by diluted acids and alkalis but strong acids and alkalis degrade it.
The solvents used for nylon 6,6 are formic acid, meta cresol CH3C6H4(OH)(also called 3-methyl phenol) and phenol. It is biological resistant and mildew bacteria have no effect.
Phenol also called carbolic acid) is an aromatic organic compound with the molecular formula C6H5OH.
Uses nylon 6,6
It has the uses like nylon 6, It is used in garments, sports goods, knitwear, also fibre clothing, tyres, shoes, umbrella, bed sheets, curtains and cushions etc.
Polyesters fiber
The most common fiber is polyester, which is a synthetic fiber. This fiber is stronger, durable, wrinkle resistance and quick dry. Polyester is the most widely used fiber is relatively cheap and can be blended with other fibers. From year 2002 Polyester the most common fiber surpressing cotton fiber.
The raw material used for polyester is terephthalic acid and glycol. Also, the process of preparation is called zeimeran process.
Hence, there are two molecules of glycol and one of the terephthalic acids.
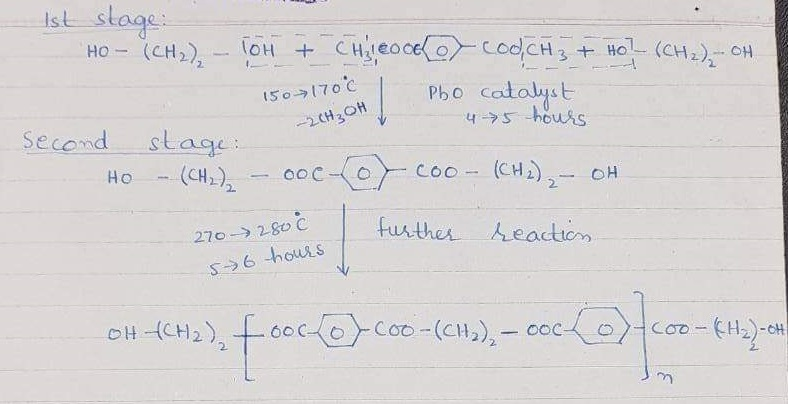
This polymer’s whole molecular weight is 20,000 and is known as polyester.
Flat cloth is pure polyester. Also, Polyester is blundered with cotton. So, the mixing which is not separated is called blend. While the methods for blending are a Blow room and Drawing frame blending. Also, the ratio of blending is different given fabric, K.I polyester, Trivera, Textron, Dacron, tefelan and many others.
Properties of polyester fibre
Tenacity 4.5 ~7.5 g/denier
Elongation at break 7.5 ~ 25%
Moisture regains 0.4%
It is chemically resistant, strong and weak alkalis and acids have no effect. oxidizing agents also have no effect. Also, has a photodegradation effect.
It is biologically resistant so used for proofing from insects.
Uses of polyester fibre
It is used in garment fibres, electrical, Collation, telephone wires, seat and table covers, Tires, bed sheets and curtains etc.
Regenerated type fibres
These are those fibres whose raw material is made by nature but is not in proper form and so are called regenerated fibres. Basically raw material is the petrochemical industry. So, in regenerated fibres, cellulose is created for making in fibrous form. The proteins are also obtained for this purpose. The regenerated fibres are.
- Viscous rayon
- Acetate rayon
- Cupraammonium rayon
- Casein fibres (soybean, milk, maize etc.)
- Alginate fibres.
Viscous rayon
Viscous rayon is obtained from cellulose,(regenerated form)
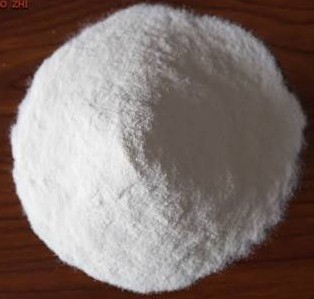
Preparation viscous rayon
In preparation, cellulose is treated with caustic soda to give soda cellulose
(alkali cellulose). The long pulp cellulose sheets are broken up from powdery crumbs(hydroxyethylcellulose), also In 2~3 days long cellulose molecules are attacked by oxygen from the air and are broken into shorter molecules.
Secondly, now alkali cellulose is mixed with carbon disulphide in a revolving drum which from cellulose xanthate orange in colour
i.e. cellulose+ caustic soda →alkali cellulose
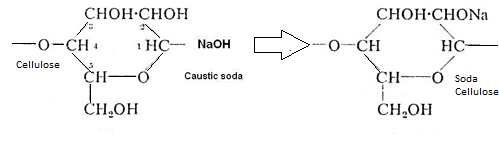
i.e. alkali cellulose +CS2→sodacellulose xanthate.
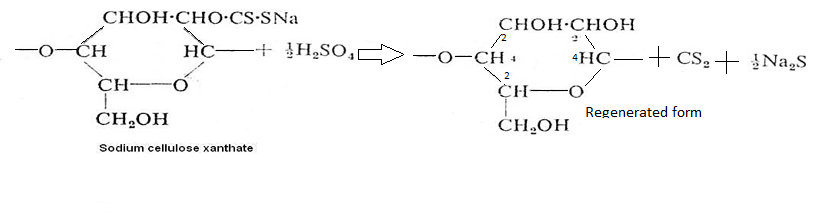
Now cellulose xanthine is treated with dill H2SO4 so unusable cellulose converts to useable cellulose.
i.e soda cellulose xanthate +dilluted H2SO4→ cellulose +NO2 SO4 +CS2(regenerated form)
The cellulose xanthate solution is allowed to stand and ripen for several days at a controlled accurate temperature, during this time filtered repeatedly viscosity of the liquid increases until it reaches a state suitable for spinning. And also bubbles of solution are removed.
Properties viscous rayon
- Tenacity 2.6 gram/denier (dry)
- Tenacity 1.5 gram/ denier (wet)
- Elongation at break 15% dry
- Elongation at break 25%wet
- Moisture regains 12~13%
- Density 1.52gram/cm3
- It is resistant to light and heat.
- It is a good insulator of electricity
- The strength of viscous rayon decreases with strong acids.
- It does not have very good biological resistance hence bacteria and insects can eat it.
- Dry cleaning agents used for viscous rayon have no effect.
- Its cross-section is irregular and so known as serrated (saw-like edges).
- Its construction has a cylindrical shape consisting of a line started.
User of viscous rayon
It has wide use in every branch of the textile industry, including carpet, furnishing, household textile, medical uses, tyres, out and underwear and many industrial uses.
Acetate rayon
Acetate rayon is obtained by acetylation of cellulose.” Also, acetylation is a process in which CH3COO group is attached and removal of any other group takes place”.
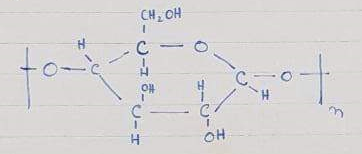
So, there are OH groups in cellulose on acetylation acetate group attaches and water is removed. Acetylation is done by glacial acetic acid which is 100% pure but for acetylation acid and anhydride are used
CH3-COOH +CH3-COOH →CH3-CO—O—CO-CH3, -H2O
Hence 100Kg wood cellulose+ 300kg glacial+ 8~10 kg pure H2SO4 as catalyst
+CH3-CO—O—CO-CH3→triacetate
i.e. temperature 8 hours 25~300C and acetic acid
i.e.
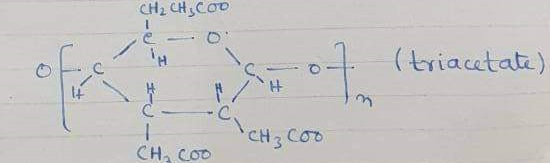
It is liquid and sometimes in solid form.
After the reaction H2SO4 is obtained in dilute formed, to stop the reversible reaction and to less reactivity of H2SO4. We add NaCH3COO and MgCH3COO
Triacetate + CH3 COOH ( anhydrous)+ H2SO4→acetate rayon
Physical properties of acetate rayon
- Tenacity 1.4 gram/denier
- Elongation at break 25%
- Thermoplastic materials
- Softens on heating
- Melting point 2300C
- Specific gravity 1.32
- Moisture regains 6.5%
- Solubility: It is soluble in acetone, and methyl-ethyl-ketone (also called MEK).
- It is a good insulator but a static charge is developed in it.
- It is biologically resistant.
Chemical properties of acetate rayon
- Strong acids and strong caustic soda degrade acetate rayon but dilute acids do not react.
- It is not affected by dilute alkalies so washing has no effect.
- It is commercially resistant, Also hydrogen peroxide and hypo-chloride are used for bleaching acetate rayon.
- Photodegradation effect: The effect of UV light is known as photo gradation. Its strength decreases to 15% After 200 hours. The decrease in strength is known as tendering.
- Structure: Longitudinal structure and also cross-section are irregular.
Uses of Acetate Rayon
It is used for curtains, ladies’ garments, bed sheets, table sheets sofa car covers etc.
Cuprammonium rayon
For the making of Cupra-rayon, cellulose is treated with a mixed solution of copper salts and ammonia, called cuprammonium liquor.
i. e. cellulose + ammonium liquor+ CuSo4 solution → cellulose (dissolved)
Dissolved cellulose +dill H2SO4 → cellulose +Cu+(NH4)2 SO4
This cellulose is again used.
Properties of cuprammonium rayon
- Tenacity =2.3 gram /denier (dry)
- Tenacity = 1.2 gram /denier (wet)
- Elongation at break =15% (dry)
- Elongation at break =25% (wet)
- Moisture regain = 11%
- In structure, its longitudinal shape is a featureless, and also cylindrical form.
- Its cross-section is regular
- Week, acids and alkalies do not attack but strong acids and alkalies react.
Uses cuprammonium rayon
This is used for making fabrics, knitwear, garments, curtains etc.