In the structure of the cotton fibre, each fibre develops as slight swelling of the epidermal layer of the surface of the seed inside the ball. Each swelling develops into a hollow tube and increases in length daily till it reaches its entire length. Up to this stage which is nearly half of its growth cycle the fibre is hollow and consists of the primary wall. In the second stage of fibre development, secondary layers of cellulose are deposited on the inside of the primary wall daily. Once such a layer is deposited each day in the form of reversal spirals. Sweller cross-section of the fibre shows daily growth of rings of 0.2-micrometre thickness. Those rings are caused by differences in cellulose structure between day and night. If cotton is grown under constant artificial light rings are not formed.
Longitudinal structure of the cotton fiber
Longitudinal structure of the cotton fibre as a ribbon-like strand with twist and reversal or a collapsed twisted tube. However, its length is 1/2″ to 2″ and its thickness is around 3~15 microns depending upon its variety and climate condition. A large number of convolutions usually 60 per centimetre are found. The twist in fiber is called convolution. These convolutions give an uneven surface to fiber, causing friction of fiber which gives adequate increase strength in spun fiber. Flat twisted ribbon but has a lower number of convolutions also looks like in immature cotton. longitudinally mature cotton fibers have three parts.
Base/root
It is a short fragile coned-type portion which during the growth of fiber remains constant, in the epidermal of seeds. It is broken in the ginning process and rarely found in commercial cotton fibers
Body
This is the main portion of cotton fibre about 3/4 of the total length. It has the same diameter throughout and has thick walls and narrow Lumen.
Tip
It is a straight narrow portion at the end of the fibres about 1/4 of the fibre length. It is very small in diameter.
The cross-sectional structure of the cotton fiber
The cross-sectional structure of cotton fibers has been studied for nearly a century also, which is shown as multilayered. Cotton fiber structure consists of the primary wall (cell) of the cotton fiber, and the outer surface layer (the cuticle) particularly, has a large influence on fiber properties. Cotton fiber has a fibrillar structure which also consists of a primary wall, a secondary wall, and a lumen. cross-sectional cotton fiber has the following parts as shown in Fig
Cotton Fiber Cuticle
Mature cotton fiber contains the following outermost layer of waxy which may also contain pectin and protein material. It serves as a smooth water-resistant coating and protects the rest of the fibre. Basically, this layer is needed to be removed from the fiber by scouring
Primary Wall of Cotton Fiber
Firstly it is the waxiest material which is formed in the early days of growth during the first 15–18 days of fibre growth. It mainly consists of cellulose but also contains pertinacious and protein material. So, the deposition of the latter begins at a very early stage, possibly on the first day of growth
Winding Layers of Cotton Fiber
As can be seen in Fig, it is the first layer of the secondary wall and differs somewhat in structure from the primary wall and the remaining is of the secondary wall.
Secondary Wall of Cotton Fiber
If we see the structure of cotton fiber under the microscope as in Fig, it consists of cellulose layers and each layer forms a concentric sheet known as a daily growth ring. Basically, in the cotton fiber under a microscope, the secondary cellulose layer is highly crystalline fibrils and microfibrils. Also, fibrils and microfibrils are extremely thin needles that spiral around the fiber axis. Basically, the secondary wall represents 90% of the total weight of fibre.
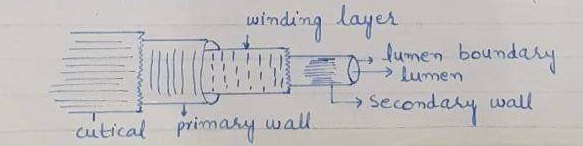
Lumen Wall of Cotton Fiber
As can be seen in cotton fiber under a microscope, the lumen wall is the boundary wall of the cavity portion inside the fiber. After the secondary wall in the cotton fiber structure is the lumen, the hollow canal that carries nutrients during growth. It also contains the dried-out protoplasm and nucleus when cotton ball development is completed.
Lumen of Cotton Fiber
It is the central cavity inside the fiber and is highly irregular in size and shape. It also contains solid matter remaining from dried protoplasm cells.
Cellulose Microfibrils of Cotton Fiber
The primary structural component of cotton fiber is cellulose. Cellulose in the cotton fiber under microscope is a long-chain microfibril called polysaccharide made up of glucose units, arranged in crystalline form. These microfibrils are highly organized and contribute to the fiber’s tensile strength.
Lignin of Cotton Fiber
In mature cotton fibers, lignin may be present, especially in the outer layers. Lignin is a complex polymer that provides additional support and rigidity to the fiber. Also, cotton fibers have distinctive surface grooves or twists, known as convolutions. This surface convolution features a high surface area which enhances absorb the ability of moisture and dyes.
Mucilage (in immature fibers)
In immature cotton fibers, mucilage is a layer of surrounds the cellulose core. It aids in seed dispersal and protection. During cotton processing, this mucilage is removed.
The unique combination of cellulose, lignin, and other components in the cotton fiber’s structure gives it the desirable properties of softness, strength, breathability, and absorbency. These properties have made cotton one of the most widely used natural fibers for textiles and various industrial applications
Chemistry of cotton fibers
Chemical composition of cotton fibers as a blow
Cellulose | 80-85% |
Nitrogenous material | 1~2.8% |
Oil and waxes | 0.5~1% |
water | 6~8% |
Pectic material | 0.4~1% |
Colour Pigment | 3~5% |
Minerals | 0.8~1.8% |
Degree of polymerization of Cotton Fiber
After scoring cotton fibre 99% of cotton is cellulose. Cellulose is a polymer made up of long chain molecules linked together with a carbon-oxygen bridge after eliminating water also called a glycol bond. Basically, there is the anhydrous bridge of the cellulose unit to form a polymer chain. So, this repeating unit of cellulose is called “degree of polymerization“.
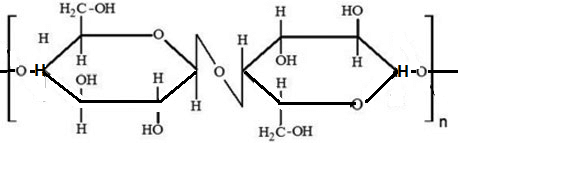
Degree of crystallinity of Cotton Fiber
Other cellulose-containing cellulose (e.g. wood pulp) is different from cotton cellulose as constructed polymer. Cotton cellulose is different from wood pulp as having a high degree of crystallinity and a high degree of polymerization. So, the “degree of crystallinity” is how closely packed and parallel molecules of cellulose one.
Altogether the high degree of crystallinity and polymerization indicate the high strength of fibres. Also, in cotton, the cellulose chain is held by hydrogen bonding. So, these hydrogen bonds occur between the hydroxyl group of adjacent molecules and parallel and closely packed molecules in the crystalline area of cellulose.
Reactive hydroxyl group of cotton fiber
Hence you can see the picture above, In the structure, three molecules of hydroxyl group, one in primary and two in secondary in each repeating unit of cellulose make it more chemically reactive. So, the groups undergo a reaction with dyes and in finishing result in modified cellulose fiber. Also, these hydroxyl groups serve to absorb moisture for water molecules. Water is chemisorbed on direct hydrogen bonding and a hydroxyl group.
In regenerated generally, the strength of cellulose fibre decreased with an increase in moisture content but can cotton fibre strength increased with an increase in moisture content. This difference is due to cellulose inter molecule bonding and the degree of crystallinity
Degree of crystallinity and polymerization of fibre(cellulose) | ||
Fibre | The average degree of polymerization | The average degree of crystallinity% |
Cotton | 9000~15000 | 73 |
Wood pulp | 600~1500 | 35 |
Viscose Rayan | 250~450 | 60 |
High tenacity | 500~650 |
Thermoplastic fiber melts during high temperatures resulting in brittle and glass transition at some point below the melting point. Also, at glass transition temperature thermoplastic becomes brittle and loses its elasticity. So on the opposite, cotton fiber doesn’t melt like thermoplastic fiber and remains very flexible at very low temperatures. Also at high-temperature cotton fibre decomposes instead of melting. Long exposure to dry heat of 300 0F(1500C) will result in fiber start decomposing slowly but exposure to high dry heat of about 4000F(2500C) causes rapid decomposition.
cotton Pre-treatment
Cotton pretreatment refers to the numerous processes applied to cotton fibers before they go through further treatments, similar to printing, dyeing, or finishing. The main objective of pretreatment is to update the cotton fibers to get the desired characteristics and improve the overall quality of the final textile product.
Pre-treatment of cotton has key benefits such as overall quality parameters and performance benefits, also,
- Improved absorbency
- Enhanced dyeability
- Increased fabric uniformity
- Fabric drape
- Improve strength
Bleaching of Cotton Fiber
Cotton fibres have or stains and natural color variations. This stain needs to be removed to achieve a sweet-sounding whiteness. Bleaching agents used are hydrogen peroxide or sodium hypochlorite, to remove the stains and natural color pigments. Since, resulting in a uniform and brighter fabric.
Scouring of Cotton Fiber
Removal of dirt, natural residual chemicals, oils, and waxes such as impurities/ contaminations. This process is called scouring. The process involves treating the fabric with alkaline solutions or surfactants. To ensure the cotton is thoroughly cleaned is done rinsing.
Mercerization of Cotton Fiber
Mercerization is a process of enhancing the luster, dyeability, and strength of cotton fibers. This process involves treating the fabric with a strong alkali solution. Mercerization of cotton fiber is done under controlled tension typically sodium hydroxide. Theprocess of mercerization of cotton fiber allows cotton fibers to swell. Also, resulting in improved properties and increased surface area.
.